
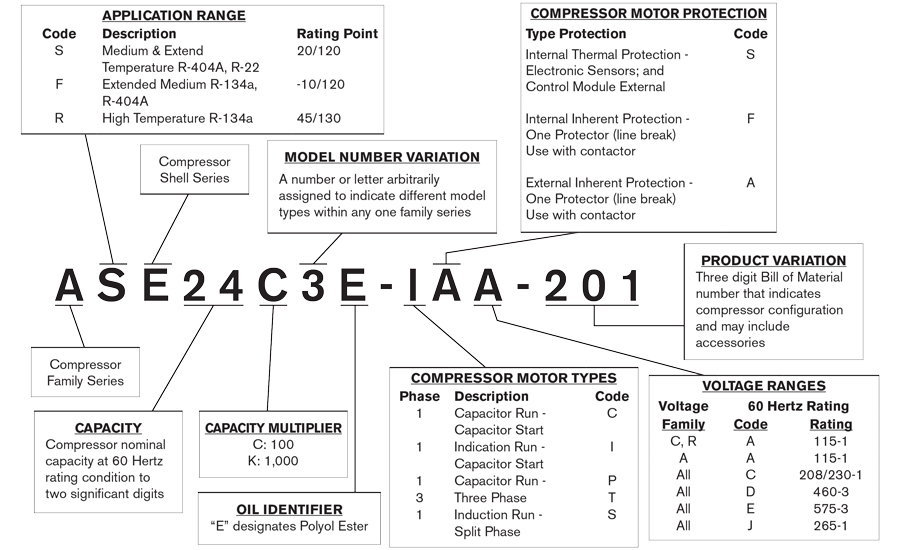
That second “02” can be any 2-digits, and it selects the wear offset to use. “Why is the “02” repeated twice?” you wonder. Now that we know about these offsets, let’s take a look at specifying a toolchange on a lathe using Fanuc’s syntax. Fanuc-Style Combined Tool Number and Offset for Turning When you do your tool change, your machine controller will automatically apply the Geometry Offset based on the information contained in its tool table about each tool. Let’s ignore the Wear Offset for the moment. To correct, you can enter a wear offset of -0.0013 to cause the machine to come out much closer to the desired tolerance. For example, you may be turning a part to diameter and discover that after measuring the diameter with a micrometer it is slightly off. The Wear Offset is a fine tuning change to the overall tool length that is used to compensate for wear and to give the machinist the ability to fine tune what’s happening from part to part. The Geometry offset is associated with each tool by number and is the one that grossly determines tool length. Now what about that business of selecting a Tool Offset so the machine knows how long the tool is?įirst thing to note is that there are actually 2 different length offsets–the Geometry Offset and the Wear Offset.
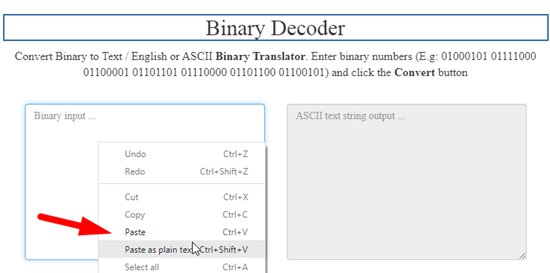
The machine keeps track of which slot T02 is actually in, for example, and you can always refer to it as “T02” Instead, the machine just sticks the tool in the nearest pocket so it doesn’t have to take so long to rotate a pocket into position. One trick some machines use to make tool changes go even faster is to set it up so tools don’t have to go back into a particular pocket on the changer. (Machining with T12 in spindle, but T14 is ready for next M06)
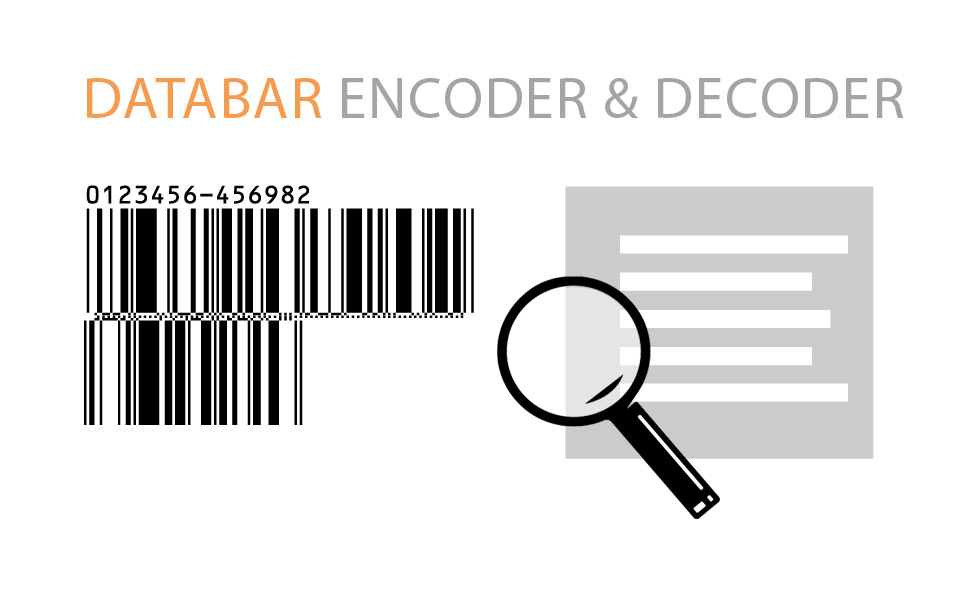
If you wanted to take advantage of the separate T and M06 to give your machine maximum time to get ready in order to make the tool change faster, you’d do something like this: If the machine doesn’t use M06, the sample would look like this: On those machines, it is likely an error to use an M06. On most lathes, and even for some mills, the M06 is not needed. This gives the ATC a little bit of advanced warning, allowing it to rotate the new tool into position while the machine is busy doing something else, which can make for a faster tool change. On a VMC with ATC, usually the “T” word tells the mill to select that tool, but it requires the M06 word to be executed before the tool is actually changed. The “T” word is commonly used to select a tool. Let’s go through each possible g-code and it’s style of use. It will adjust its notion of where the tool tip is when you make your next move based on this.Īccomplishing these two functions can require anywhere from one to several g-codes. The tool length offset tells the CNC machine how much the length of the current tool differs from tool #1. The second role of these codes is to set up a different tool length offset. First, in the case of a machine with an automatic tool changer (ATC), the tool changing g-codes tell the ATC to load a particular tool in the spindle or, in the case of a lathe, to rotate that tool into position on the lathe’s turret. That’s because the tool change programming serves two purposes. This will be true even if your machine doesn’t have an automatic tool changer. Most CNC g-code programs will have one or more g-code tool changes programmed into them. Tool Changes and Tool Offsets in G-Code CNCCookbook’s G-Code Tutorial G-Code Tool Changes
